CH-Bioforce strives for a cleaner world with unique BIOFORSENSE® technology
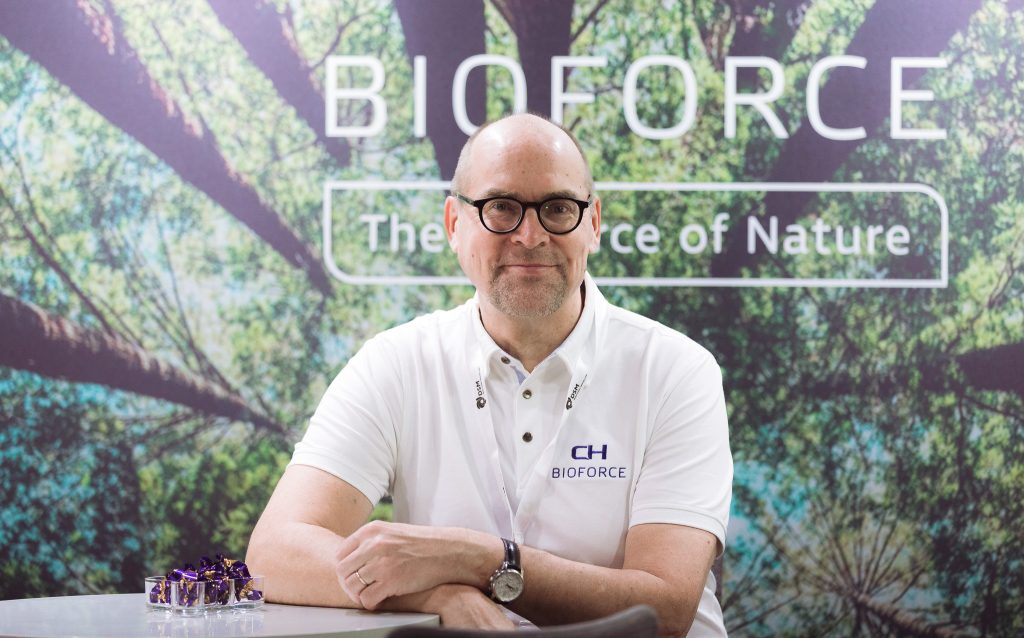
In this interview, Petri Tolonen, CEO of CH-Bioforce, sheds light on the environmental benefits of BIOFORSENSE® technology. The article is originally published in Open Access Government in 16th January 2024.
Bio-based side streams to end industrial waste increase
In a world where the demand for sustainable and eco-conscious products continues to surge, manufacturers face the task of redefining their operations and approaches to align with sustainability goals.
CH-Bioforce stands at the forefront of this movement, ready to meet the surging demand with its innovative BIOFORSENSE technology.
BIOFORSENSE technology is designed for nearly chemical-free processing of various biomass types such as wood and straw. This process yields exceptionally pure biomaterials – CELLENSE™ (cellulose), XYLENSE® (hemicellulose), and LIGNENSE® (lignin). These sustainable materials can replace fossil-based raw materials and cotton as binders, fillers, emulsifiers, textile fibres, and even components in medical applications.
In this interview, Petri Tolonen, CEO of CH-Bioforce, sheds light on the environmental benefits of BIOFORSENSE technology.
“We use industrial side streams as a raw material – we are turning waste to value. Our technology is very environmentally friendly, carbon neutral, and uses fewer chemicals and fresh water than conventional biomass fractionation processes.
“The customers can use our biomaterials without decreasing product useability or durability. The products maintain their features while the manufacturing produces less CO2 emissions, emits fewer microplastics into the world and decreases the demand for fossil-based raw materials,” says Tolonen.
What sets BIOFORSENSE apart is that it’s the only solution out there that gently extracts all the major biomass components in a single process, Tolonen notes.
“BIOFORSENSE technology is not restricted to any specific raw material – the opposite is, in fact, true. The technology can extract biopolymers from wood and other lignocellulosic feedstock, like agricultural and industrial side streams. By 2025, it’s predicted that the industrial biomass waste market size will be tens of billions of U.S. dollars annually, and this estimate is increasing rapidly,” Tolonen adds.
Solving a global problem
Modern consumer industries heavily rely on fossil-based raw materials, while many agricultural side streams, like straw, are burned in the worst case. This wasteful practice results in billions of tons of greenhouse emissions globally, whereas these side streams could replace harmful or fossil-based components in the manufacturing process, Tolonen notes.
“This doesn’t have to be the status quo. We want to change that. We aim to turn waste into high-value raw materials for our planet’s sake. Our technology is already making this a reality,” Tolonen emphasises.
“The world is drenched in non renewable waste. Microplastics are present in rivers, seas, and lakes, while greenhouse gases alter the climate and overexploit our fragile environment. We yearn for a world free of plastic waste and fossil-based consumer goods that harm the planet.”
The consumer demand is clear
Today’s consumers demand more sustainable goods and apparel. Simultaneously, regulations and legislation, like the EU Single-Use Plastics Directive, drive manufacturers to locate renewable, bio-based raw materials for their products. CH-Bioforce has already addressed this need through collaborations with various partners.
“Manufacturers want to use the raw material as efficiently as possible. We can further enhance the utilisation of cellulose-containing raw materials by using the generated side streams as raw materials. In the best case, the customer can use the resulting products in their own production.
“For example, let’s mention the production of flour from grain. In this case, the husk of the grains often goes unused. For example, hemicellulose can be made from the husk material, which can be used as a health promoting nutrient in foods.
“For example, cellulose can be a sustainable alternative for textile fibre production, replacing cotton-based textiles. We have partnered with companies like Spinnova, who create sustainable materials for clothing brands such as Marimekko. We are also active in the cosmetics industry, as seen in a recent project with the HETKINEN lifestyle brand that produced promising results.
“Right now, CH-Bioforce is on the cusp of a significant development leap.
“We are building our production plant, enabling us to undertake increasingly larger projects. We are collaborating with global partners, and many exciting discussions are underway. The importance of our technology is undeniable,” Tolonen concludes.
It all started in Raisio, Finland
In 2011, Nicholas Lax, Sebastian von Schoultz and Lari Vähäsalo, both wood chemistry specialists, discovered that utilising vacuum and ensuring precise chemical control made it possible to extract hemicelluloses in purity and high yield in their native polymeric form.
After a few years of experiments, they further developed their findings and established CH-Bioforce in 2016. Now, the company is operating globally and looking towards its most significant development steps with its own production facility.
News
- CH-Bioforce attending the leading global event of the cosmetics industry: in-cosmetics Global
- CH-Bioforce strives for a cleaner world with unique BIOFORSENSE® technology
- CH-Bioforce’s annual donation for climate and nature
- CH-Bioforce to Present Bioforsense Technology at The Greener Manufacturing Show 2023
- Ecological Cosmetics Move from Niche to Mainstream
- Pure and ecological clean beauty from Finland
- CH-Bioforce is attending the leading global cosmetics industry event: In-Cosmetics Global 2023 in Barcelona, Spain
- CH-Bioforce to receive up to €15 million in funding from European Innovation Council
- A donation for our climate and nature
- PI Challenge Hackathon Inspired Us Towards The Future
- Woodly To Join In Collaboration With CH-Bioforce For Future Projects
- CH-Bioforce Awarded the Entrepreneurial Spirit of Turku Prize
- Petri Tolonen to lead CH-Bioforce
- CH-Bioforce Shortlisted for New Energy Challenge 2020 Competition
- Molar mass of lignin is the key factor in the production of a high-performance phenol replacement
- CH-Bioforce helps world’s biggest brewing company turn brewing waste into textiles
- Three scientists and a garage – This is how it all started
- Straw as a promising sustainable feedstock option for the production of bio-based polymers
- Towards a circular bioeconomy: lignin as a renewable alternative to chemical industry
- Towards a circular bioeconomy: natural polymers to stabilise technical emulsions
- CH-Bioforce receives over €2 million grant from EU’s Horizon 2020
CH-Bioforce Oy
CH-Bioforce Oy is a Finnish start-up founded in 2016. The company’s innovative fractionation technology dates back to 2011, when inventors Lari Vähäsalo, Nicholas Lax and Sebastian von Schoultz made their first findings. Today, the company forms part of the Chemec group, which operates in the chemical industry. CH-Bioforce currently employs ten members of staff. Our R&D and pilot plant is located in Raisio, Finland.
For more information
Petri Tolonen
CEO, CH-Bioforce Oy
+358 9 502 4410
petri.tolonen@ch-bioforce.com